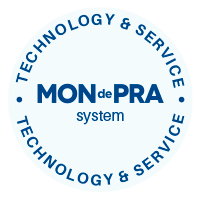
Our exclusive
manufacturing system
Eight layers carefully manipulated to offer our exclusive patented manufacturing system.
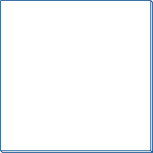
Layer 1
Gel Coat ISO NPG (high neopentylene glycol load)
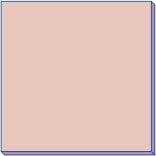
Layer 2
Mat 300 laminate with high chemical resistance resins
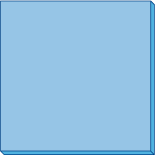
Layer 3
Sandwich laminate of MATs interwoven with isophthalic resins
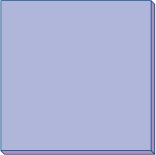
Layer 4
Sandwich laminate of MATs interwoven with isophthalic resins
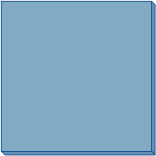
Layer 5
Sandwich laminate of MATs interwoven with isophthalic resins
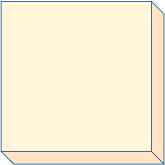
Layer 6
Steel skeleton in the vital parts of the hull
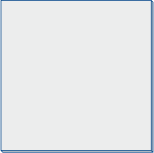
Layer 7
Projected reinforcements and skeleton made from recycled materials.
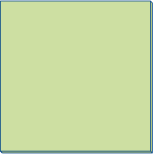
Layer 8
Total resin impregnation with environmentally friendly paraffin agents for the preservation of the environment.
-
Layer 1
Gel Coat ISO NPG (high neopentylene glycol load)
-
Layer 2
Mat 300 laminate with high chemical resistance resins
-
Layer 3
Sandwich laminate of MATs interwoven with isophthalic resins
-
Layer 4
Sandwich laminate of MATs interwoven with isophthalic resins
-
Layer 5
Sandwich laminate of MATs interwoven with isophthalic resins
-
Layer 6
Steel skeleton in the vital parts of the hull
-
Layer 7
Projected reinforcements and skeleton made from recycled materials.
-
Layer 8
Total resin impregnation with environmentally friendly paraffin agents for the preservation of the environment.
Always one piece
All models in one piece made of polyester, with no joints or unions, thus creating a structure that is completely resistant to the movements and alterations of the ground.
Anti-leak
We are pioneers in the use of our own maximum resistance nozzle system. In the unlikely event of a leak, these can be changed from the interior without the need for external work.
High quality
We work with highest-quality materials. The best polyester resins on the market (used in the aerospace, nautical and wind power industries) reinforced with fibreglass guarantee maximum resistance to chemical agents.
Handcrafted
The whole lamination and reinforcing process of the unit is performed manually to achieve the maximum mechanical resistance of your pool.